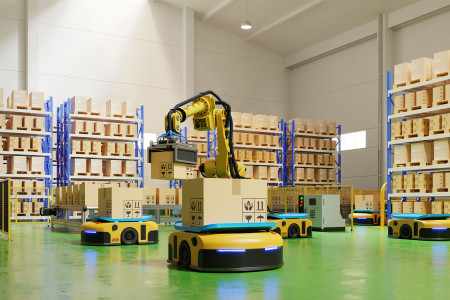
Introduction:
The Warehouse Control System Market has undergone significant transformation in recent years. With the rise of e-commerce and the increasing demand for faster, more efficient order fulfillment, WCS solutions have evolved from simple automation tools into complex, intelligent systems that help businesses streamline their warehouse operations. As technology advances and customer expectations continue to grow, WCS solutions have become an integral part of modern supply chain management. This article explores the evolution of Warehouse Control Systems, highlighting the journey from basic automation to intelligent warehouse operations, and examines the factors driving the shift in the WCS market.
The Early Days of Warehouse Control Systems
Warehouse Control Systems have been around for decades, with their roots tracing back to the 1970s and 1980s when basic automation began making its way into warehouses. At that time, WCS solutions were primarily used to manage material handling equipment such as conveyors, lifts, and sorting machines. These systems were designed to automate repetitive tasks, reducing the need for manual labor and increasing operational efficiency.
However, these early WCS solutions were relatively limited in their capabilities. They typically operated in isolation, focused on controlling specific pieces of equipment or machinery within a warehouse. While this automation helped warehouses become more efficient, it lacked the intelligence to optimize the entire operation. Warehouse managers still had to rely on manual intervention and decision-making to resolve issues, and the systems had limited flexibility or scalability.
The Rise of Integrated Systems: Early Automation and Software Integration
As warehouses grew in size and complexity, the need for more integrated and sophisticated control systems became apparent. In the 1990s and early 2000s, WCS solutions began to evolve beyond simple automation. The focus shifted toward integrating different components of warehouse operations, such as inventory management, order fulfillment, and material handling.
At this stage, WCS systems started to incorporate Warehouse Management Systems (WMS) and other enterprise software solutions. The integration of WMS with WCS allowed warehouses to more efficiently manage stock levels, track inventory, and optimize the picking and shipping processes. The synergy between WMS and WCS improved decision-making by enabling real-time visibility of inventory and streamlining the flow of goods through the warehouse.
However, these integrated systems still lacked advanced intelligence, and the focus remained on automating routine tasks. Warehouse managers were able to optimize certain processes but still needed to monitor and adjust systems manually when unexpected disruptions or inefficiencies arose.
The Emergence of Advanced Automation and Real-Time Data Integration
The next phase in the evolution of WCS came with the emergence of advanced automation technologies and real-time data integration. As the internet, cloud computing, and the Internet of Things (IoT) became more prevalent in the 2010s, WCS solutions became more sophisticated and connected. The adoption of these technologies enabled warehouses to collect vast amounts of real-time data from various sources, including sensors, RFID tags, and other connected devices.
This influx of real-time data opened the door to smarter, more agile WCS solutions. By integrating IoT devices, WCS systems could monitor the condition of equipment, track inventory more accurately, and adjust operations in real time based on changing demand or workflow disruptions. For example, if an item in the warehouse was running low or out of stock, the system could automatically adjust the picking process to ensure that orders were filled on time.
Another breakthrough during this period was the incorporation of robotics and automated guided vehicles (AGVs) into warehouse operations. WCS systems became capable of controlling and coordinating a wide range of robotic equipment, such as picking robots, sorting machines, and AGVs. This increased automation further reduced the need for manual labor and streamlined workflows, allowing for faster order fulfillment and greater throughput.
Moreover, real-time data integration allowed warehouse managers to make data-driven decisions and respond to operational issues faster. Instead of waiting for human intervention, WCS systems could automatically adjust workflows, prioritize tasks, and re-route inventory to minimize delays.
The Shift to Intelligent Warehouse Operations: Artificial Intelligence and Machine Learning
As the demand for even greater operational efficiency and optimization increased, WCS solutions began to incorporate Artificial Intelligence (AI) and Machine Learning (ML) in the late 2010s and into the 2020s. These technologies revolutionized the WCS market by providing the intelligence needed to make predictive and proactive decisions, rather than just reactive ones.
AI and ML algorithms enable WCS systems to analyze historical data, identify patterns, and make predictions about future demand, inventory needs, and potential bottlenecks. This has led to significant improvements in warehouse operations, including better demand forecasting, optimized inventory management, and more efficient picking and packing processes. For instance, ML algorithms can analyze trends in order volume and adjust staffing levels or equipment usage accordingly to ensure that the warehouse operates at peak efficiency.
Another key development in intelligent WCS systems is the use of advanced analytics and optimization algorithms. These systems can continuously analyze vast amounts of operational data in real time, identify inefficiencies, and recommend changes to improve throughput and reduce costs. Warehouse managers can now rely on intelligent WCS solutions to identify issues such as underutilized equipment, inefficient picking routes, and suboptimal inventory levels, helping them make informed decisions and enhance overall performance.
AI-powered WCS systems are also improving the ability of warehouses to handle complex tasks, such as multi-channel order fulfillment. With the rise of omnichannel retail, warehouses must be able to handle orders from both online and brick-and-mortar customers seamlessly. Intelligent WCS solutions allow for better coordination between different fulfillment channels, ensuring that orders are picked, packed, and shipped efficiently, regardless of the source.
The Role of Cloud Computing and Scalability in Modern WCS
Cloud computing has played a significant role in the evolution of WCS by offering scalability, flexibility, and cost-efficiency. In the past, on-premise WCS solutions were the norm, requiring significant upfront investments in hardware, software, and infrastructure. However, with the rise of cloud-based WCS solutions, warehouses can now access advanced control systems without the need for heavy capital expenditures.
Cloud-based WCS platforms offer numerous benefits, including the ability to scale operations up or down based on demand, seamless integration with other enterprise systems (such as WMS, Enterprise Resource Planning, and Customer Relationship Management systems), and real-time data access from anywhere. This is particularly important for businesses with multiple warehouses or global operations, as cloud-based WCS solutions can be centrally managed and updated, reducing the need for on-site maintenance and ensuring that systems are always running at optimal performance.
Additionally, cloud-based WCS solutions enable better collaboration across supply chain partners, allowing for greater transparency and efficiency in inventory management and order fulfillment.
The Future of Warehouse Control Systems: Towards Fully Autonomous Operations
Looking ahead, the future of Warehouse Control Systems will likely involve even more advanced automation, intelligence, and integration. The rise of autonomous technologies, such as autonomous mobile robots (AMRs), drones, and fully automated storage and retrieval systems (AS/RS), will further transform the WCS market. These technologies will allow warehouses to operate with minimal human intervention, dramatically increasing efficiency and reducing errors.
Furthermore, the integration of AI and IoT technologies will continue to evolve, enabling even more sophisticated systems that can self-optimize, predict disruptions, and autonomously adjust workflows. As supply chains become more complex and demand for faster order fulfillment grows, the role of intelligent WCS solutions will become even more critical in ensuring smooth, efficient operations.
Conclusion
The evolution of Warehouse Control Systems from basic automation to intelligent warehouse operations has been driven by advances in technology, including AI, machine learning, robotics, and cloud computing. As the WCS market continues to mature, businesses are increasingly adopting more sophisticated and integrated systems that enable greater efficiency, flexibility, and scalability.
The future of WCS will be defined by even greater levels of automation, intelligence, and connectivity, allowing warehouses to operate with minimal human intervention while optimizing their operations for speed, accuracy, and cost-efficiency. As businesses strive to meet the demands of the modern supply chain, intelligent Warehouse Control Systems will play a pivotal role in driving operational success and maintaining a competitive edge in an increasingly fast-paced and dynamic market.
Write a comment ...